According to Texas A&M, researchers have significantly developed a new bonding technology – interlocking metasurfaces (ILMs) – using 3D printing. In collaboration with Sandia National Laboratories, ILMs are designed to increase strength and structural stability compared to traditional methods such as bolts and adhesives, using shape memory alloys (SMAs), and giving the opportunity to change the integrated design of the machine to produce. for aerospace, robotics, and biomedical applications. Research can be found in Materials & Design.
“ILMs are committed to redefining the integration of technology across a wide range of applications, just as Velcro did decades ago,” said Dr. Ibrahim Karaman, Professor and Head of the Materials Science and Engineering Department at Texas A&M. “In collaboration with Sandia National Laboratories, the leading manufacturers of ILMs, we have developed and manufactured ILMs from structural concept alloys. Our research shows that these ILMs are can be selectively removed and recaptured on demand while maintaining cohesive strength and structural integrity.”
Like Lego or Velcro, ILMs help connect two bodies by transferring force and restricting movement. So far, this method of integration is not working – it needs power for commitment.
Using 3D printing, the teams created and manufactured functional ILMs by combining shape memory alloys (SMAs), mainly nickel-titanium, which can return to its original shape with after changing the temperature by changing the temperature.
The control of combining technology with temperature changes opens up new opportunities for smart, adaptive buildings without loss of energy or stability and with an increase in options for flexibility and performance.
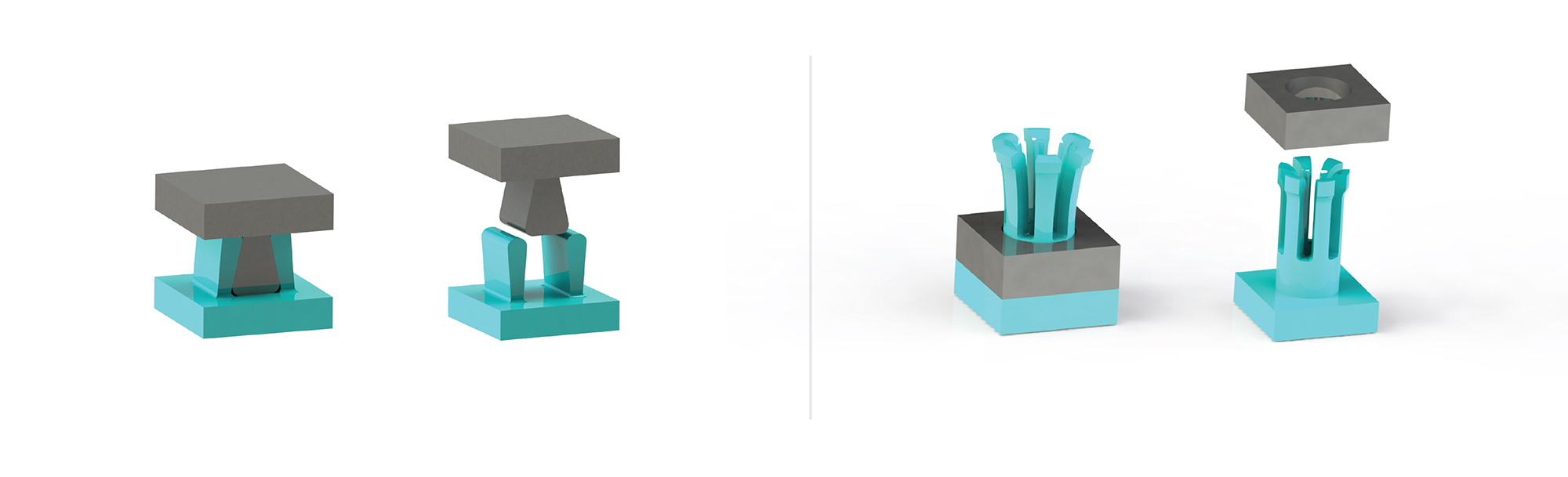
“Active ILMs have the potential to revolutionize complex mechanical designs in industries that require precise, repeatable assembly and disassembly,” said Abdelrahman Elsayed, assistant researcher in the Department of Materials Science and Engineering at Texas A&M. .
Practical applications include designing aerospace engineering components where parts must be assembled and disassembled many times. Functional ILMs can also provide flexible and flexible joints for robotics development. Biomedical devices, the ability to adapt implants and prosthetics to body movement and temperature can provide better options for patients.
The present study used the concept of the formation of SMAs to reverse the formation of ILMs by increasing the temperature. The researchers hope to build on these findings by exploiting the superelasticity effect of SMAs to create ILMs that can withstand large deformations and recover instantly under extreme conditions. especially stress.
“We expect that incorporating SMAs into ILMs will open up many future applications, although there are still many challenges,” said Karaman. “Achieving superelasticity in 3D printed ILMs will enable local control of structural stiffness and facilitate reassembly with high locking forces. In addition, we expect this technology to address the challenges of long-term contact methods at extremes. We are passionate about the transformative power of ILM technology.”
Other contributors include Dr. Alaa Elwany, the Wm Michael Barnes ’64 Assistant Professor in the Department of Industrial and Process Engineering, and doctoral student Taresh Guleria in the Department of Industrial and Process Engineering.
Funding for this research is administered by the Texas A&M Engineering Experiment Station (TEES), the official research center of Texas A&M Engineering.
#Researchers #developing #assembly #technology #printing